What is
mass concrete
Mass concrete refers to volumes of concrete large enough to generate significant heat and temperature differentials during the hardening process. Heat and temperature differentials can cause issues with:
- structural integrity,
- longevity and
- appearance.
All concrete generates heat through hydration. In mass concrete, the heat generated varies depending on the location within the pour and the degree of insulation from the surrounding concrete, formwork and insulation. Higher temperatures accelerate the rate of hydration, thus the rate at which heat is produced.
Failure to manage the thermal process of mass concrete pours can impact structural integrity, durability and serviceability, significantly impacting project costs, timelines and risk.
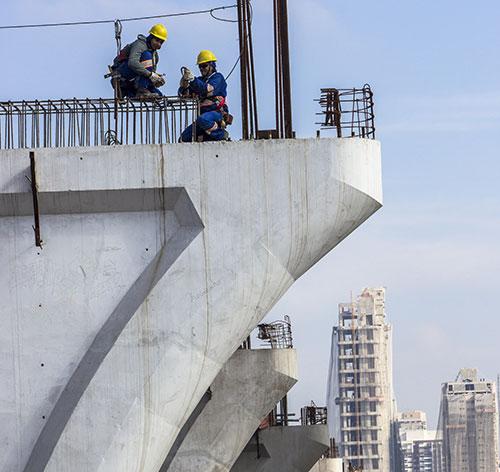
Peak temperature
- If the internal temperatures of concrete exceed predetermined limits, typically 70ºC (158ºF) to 80ºC (176ºC) depending on binders used, the structural integrity and long term durability of some concrete structures can be effected - and this may not be evident for many years.
- Unless measures are taken upfront, e.g. lowering placing temperatures and cooling pipes, once concrete is poured there is really no practical way to control the rate of hydration and peak temperature generated. Therefore, it’s important to ensure precautions are taken to model, design and produce concrete which has the appropriate characteristics.
- It’s then critical to monitor the in-place temperatures to understand how the concrete is performing, and whether the maximum temperature achieved matches the modelling and is a cause for concern (bearing in mind the effects may only be apparent many years later).
Temperature Differentials
- If the temperature differentials within the elements exceed predetermined limits, thermal cracking may occur.
- Pre-planning is critical.
- If it’s detected that temperature differentials are increasing, and there’s a risk that temperature differentials will exceed critical limits, then actions can be implemented to minimise risk e.g. insulating the exposed surfaces to minimise heat loss.
- Hence, it’s essential that relevant locations in the concrete elements are monitored, to allow appropriate action to be taken, risk of thermal cracking to be minimised and to ensure the required information is available to substantiate your position.
- It is also important to monitor and manage the temperature differentials between the surface of the concrete and the ambient conditions, as stripping formwork etc. When these differentials are too great, cracking can occur due to thermal shock, which can rapidly increase internal differentials and the risk of thermal cracking.
- Monitoring mass concrete elements should not simply be a case of ticking boxes. Proper management, using real time solutions, allows compliance to be verified while minimising the risk of costly issues and optimising construction cycles.
conXedge is a comprehensive solution
measure and manage concrete temperature and strength for both Concrete Maturity and Mass Concrete in real time.